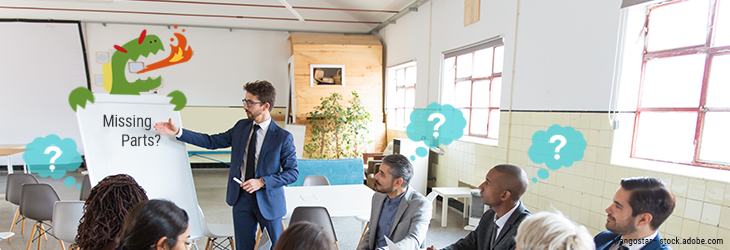
Grappling with the problem of missing parts has become a daily routine in most companies. The parts hunters are once again on the hunt, equipped machines are disarmed, the production plan is shot down - all to get the missing part produced as soon as possible. But hold on! Is that the right way to go about it?
As a rule, the assembly department is the last to hear if a part is missing or will go missing. However, if you retrace all the steps along the information chain it should have become apparent much earlier that this part would go missing. The question is…why didn’t we realize this?
In my consultancy work, I often notice that in such a situation....nothing happens. Partly due to ignorance or out of a false sense of security. The tendency is not to report the „anomaly“ because one believes that the part will probably become available by the actual requirement date. One operates according to the “principle of hope“: it will all work out – there’s surely enough time....
And we all know about all the things that can happen in production and how difficult it is to keep deadlines. So, for missing parts, the big question is: at what point does a “part” become a “missing part”? When it’s already missing in assembly, or when you realize it could go missing?
Frontloading - pro-active missing parts management
The principle of frontloading is basically defining report points along the entire supply chain for cases at which deviations may occur. The entire process chain must first be standardized, and this means clearly setting out who does what, when or how, if any deviation from the plan occurs. There must be a system in place that says exactly what to do as soon as information is received that a part will go missing.
Of course, you don’t get this kind of information by just waiting for it to fall into your lap. It requires a certain amount of pro-active investigative effort. And even though this may not be possible for all parts, it must be attainable for all critical parts (those essential for purchasing or in-house production).
- Long-running projects
- Parts whose actual replenishment times are longer than specified in the article master data
- Parts with poor supplier performance
- Parts with unconfirmed delivery dates
- Parts that will be delivered later than requested
It is the task of every dispatcher or purchaser to do everything possible to see that parts are delivered exactly as scheduled. However, if it becomes clear that a part will not be available on time, then all affected departments and processes must be informed immediately. Consequently, this means adjustments will have to be made at various points throughout the plan.
Of course, this can only work if the production plan for the entire supply chain is both realistic and feasible. But more about that in the next Blog.
Autor:
Yutaka Müller-Mark, Meisterberater der KPC Production Systems Engineering GmbH
Partner company: Asprova GmbH
World No.1 APS Production Scheduler
www.asprova.eu